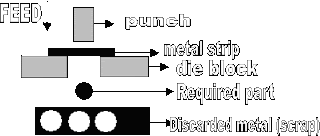
Blanking is the operation of cutting a flat shape from sheetmetal . The part punched out from the metal strip is called “blank”, and it is the required product of the operations. It is usually the first step of series of operations. After blank the metal strip called as scrap.
PIERCING (OR) PUNCHING
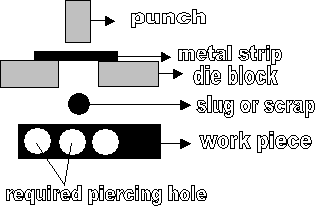
CUTTING OFF:
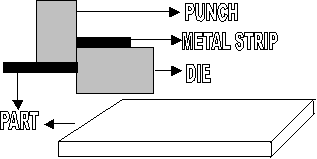
In this operation, upper blade(punch) is connected to the ram. Lower blade is fixed in machine frame. The work is placed between two blades. A slight clearance between the cutting edges of blades. When the upper blade moves it cuts off the sheet metal
PARTING OFF:
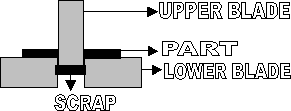
NOTCHING:
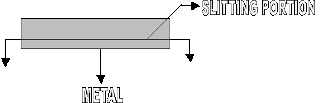
LANCING:
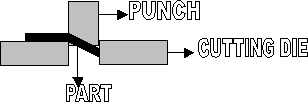
Example: Mosquito coil stand.
PEFORATING:
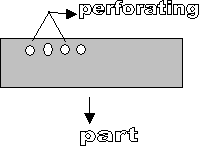
BENDING:
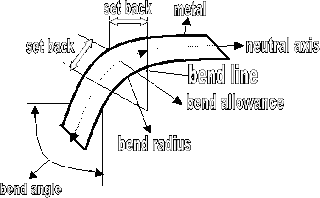
During the bending operation, the outer surface of the metal is in tension and the inside surface is in compression. The strain in the bent material increases with decreasing radius of curvature. The stretching of the bend causes the neutral axis of the section to move towards the inner surface.
V-BENDING (OR) ANGLE BENDING
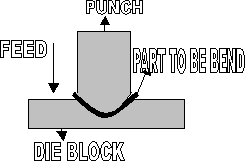
EDGE BENDING
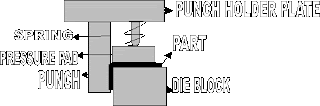
In edge bending, a flat punch forces the metal against the vertical face of the die. The bend axis is parallel to the edge of the die and the stock is subjected to cantilever loading. In this bending, a pressure pad is used, for prevent the movement of the stock during operations.
SHAVING
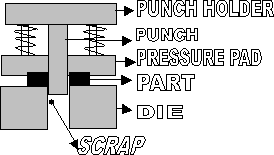
TRIMMING
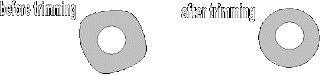
CURLING
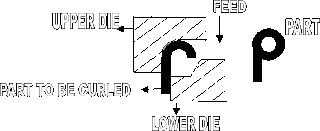
Curling is the operation of rolling the edges of the sheet metal to a small circular form. Curling is done to strengthen the edges. By curling, the sharp edges of the metal is avoided.
The lower die held stationary. The upper die has got a curved form at its end. When it moves down,the edge of the work is curled into a circle. Curling is used in making sheet metal vessals and containers
FORMING
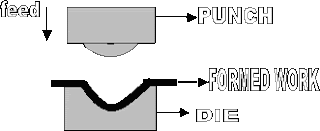
COINING
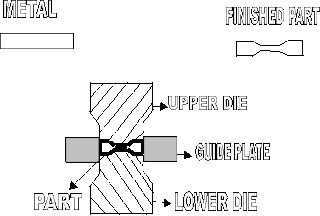
Coining is the operation of squeezing the metal between two dies. A blank of correct size is placed between the lower and upper die.Both dies are engraved to have the required pattern and shape.
Both the dies press the metal blank with very high force. The blank metal flows in the cold state and fills up the cavity between the dies. The pattern on the two dies are transferred to the component.The movement of the die is guided by a guide plate.These operations producing coins,metal and other similar parts.
EMBOSSING
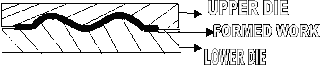
The blank is placed between two dies. The dies will have the same Impression for the required component. One die have projection and the other die have corresponding depressions. The upper die presses down the blank on the lower die. The blank metal flows in the cold state and gets the required impressions.
These operations is used on tin containers, covers and name plates.
PLUNGING
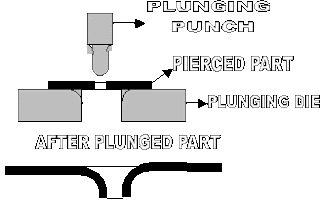
Plunging is the operation of localized bending around a hole in the sheet metal. Plunging is done in two stages. First the hole is pierced in the work at the required position using piercing punch and die. Then the hole in the sheet metal is plunged The plunged hole will take the shape of the punch and die. Plunging is done to received a screw head or rod through the holes. Plungingaremade asCountersunk, burred or dimpled holes.Plunging operation is also called as Hole flanging or Extruding.
FLATTENING OR PLANISHING
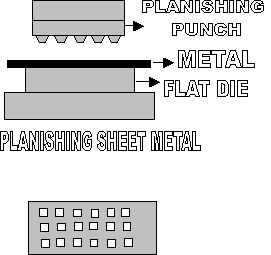
This is the operation of straightening a bent or curved sheet metal. The planishing punch has small projections on its face. The projections are spaced equally. The die has a flat plain surface.The sheet metal having bent is placed over the flat die. The punch presses the sheet metal with high pressure.The bends on the sheet metal are removed.
DRAWING OR CUPPING
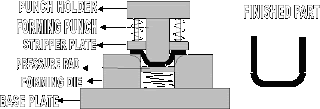
Drawing is the operation of producing cup shaped parts from the sheet metal blanks. The blank is placed over the forming die. The stripper plate is hold the blank on the die. When the punch moves down, the blank is pushed into the dieopening. A pressure pad is placed inside the die opening, which is used for uniform drawing operation.Plastic deformation takes place in the blank. The metal is drawn over the surface of the die opening. Sufficient clearance is given between the punch and die.A cup shaped components are produced by drawing operation,this process is calledCupping.
DEEP DRAWING
DEEP DRAWING
Deep drawing is the operation of producing cup shaped components having more depth. Here the depth of the component produced is more than its diameter.
Deep drawing is done in different stages,by using different sets of punch and dies. After each stage of drawing, the blank surface gets hardened. So to avoid rupture and failure, the blank is annealed before the next stage of drawing operations.